DC Batch
Automate Batch Treatments with Dynamic Scheduling
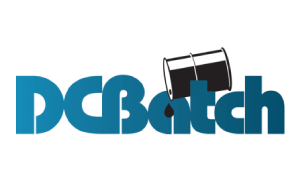
The DC3–Batch Control System allows you to automate your treater truck programs.
The DCB (DC3 Batch) system is the most comprehensive, advanced automated chemical batching system on the market. Equipped with multiple batching methods and an automated slip stream flush valve, you will have the ability to batch and treat based on any protocol you can come up with.
UNIQUE FEATURES SUCH AS:
• Multiple Modes of Operation
• Control your batch duration, and amount (qts)
• Options for pre and post flush
• Ability to batch based on accumulated production flow
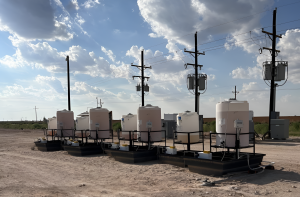
How it Works
The DC3 Batch Control System with optional flush control system operates in 3 modes. You simply enter the setpoints per the design of your batch treatment to start treatments.
Volume and interval of batch treatments are fixed and will repeat until changed.
By tracking your production over time, the volume of chemical injected during the batch will change to achieve the correct target dosage amount with a fixed interval time.
By tracking your production over time, the frequency of your batch will automatically adjust with your fixed dosage amount.
Non repeating batches that can be triggered on demand at the volume required for an ad-hoc batch treatment.
Set points for Pre-Flush, Sync-Flush and Post-Flush creates a customizable batch that mimics treater truck operations.
BENEFITS:
On-site equipment performs chemical batch treatments without pump trucks by retrofitting standard chemical injection equipment used in continuous applications.
Eliminate and compensate for pump drift, even with solar-powered systems (up to 40% daily), ensuring optimal chemical delivery.
Automatically adjusts the batch volume and/or frequency of treatments in response to changes in production.
Verification of batch treatments and volumes used.
Reduce failures and leaks by dynamically adjusting your batch program to eliminate under treatment.
A proactive approach to verify injection delivery, enhancing the reliability and effectiveness of your chemical treatment.
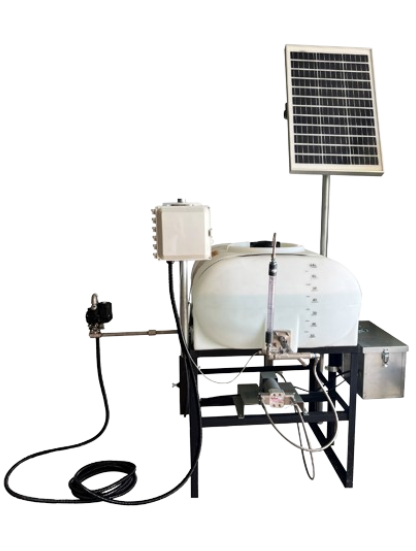
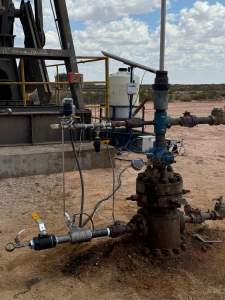
FEATURES:
Use any pump or tank, offering flexibility in diverse field conditions.
Keep a constant eye on tank levels, ensuring uninterrupted operations.
Optional flush control valve can operate in sync with batch treatments to mimic treater truck operations with pre-flush, sync-flush and post flush set points.
Using fluid from the well for diluent and carrier fluid(flush), you can minimize or eliminate the introduction of bacteria and incompatible fluids from treater tuck operations.
Dynamically adjust batch volumes and treatment intervals based on real-time flowrate changes.
Manage and control and change your batch schedule remotely or locally when.
Ad-hoc batch treatments can be triggered as needed.
Monitor and assess battery health (volts/amps), preempting power-related issues.
Easily integrate into existing SCADA systems for streamlined operations.
Access to a specialized portal for enhanced data analysis and control.
Monitor when technicians calibrate chemical pumps to maintain precise chemical injection, maintaining consistent treatment efficacy.
TECHNICAL SPECIFICATIONS:
Dimensions: 19 x 13 x 9
Area Classification: C1D2
Compatibility: Designed to work seamlessly with a variety of chemicals, pumps and tanks.
Power Requirements: 10-32 VDC, 110/120 VAC
Connectivity: RS485, TCP-IP, Integrated SignalFire 900MHz radio. DC3 cloud portal optional
Material & Build: Constructed with 304SS, 316SS Teflon wetted parts, additional material available
Environmental Tolerance: Designed to operate efficiently in -40C – 85 C, making it suitable for diverse field applications.
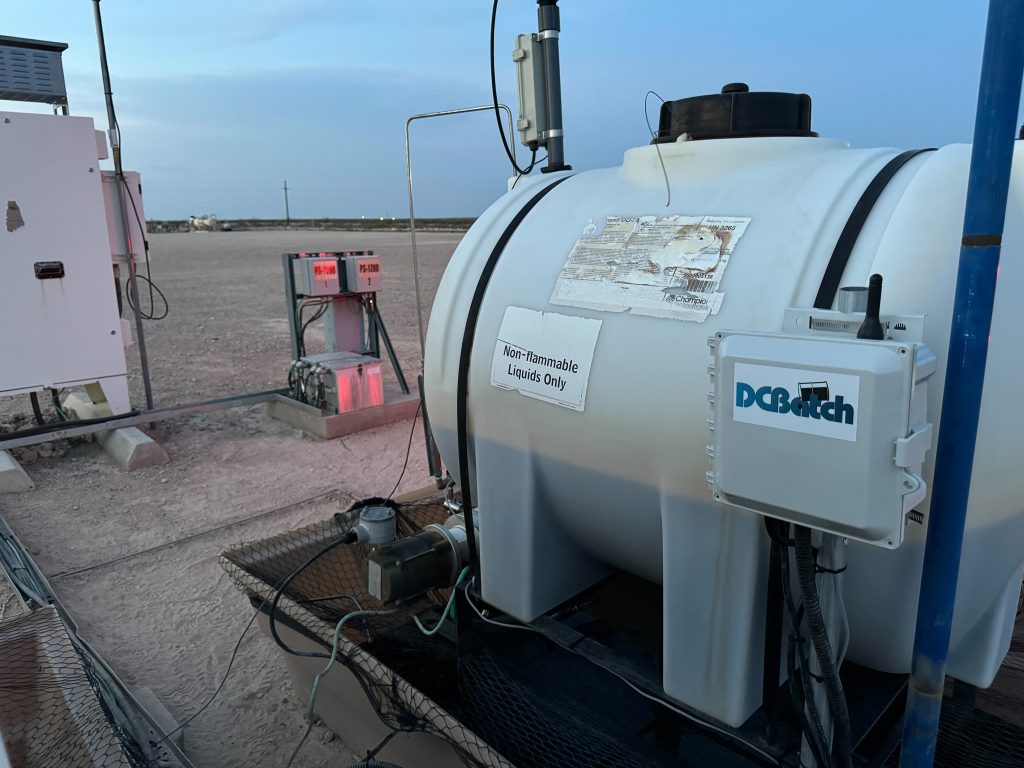
Frequently Asked Questions
DCBatch offers four treatment modes: Batch Auto Vol (injection schedules), Batch Auto Track-Time (treats based on total production), Batch Auto-Track-Volume (doses based on production and ppm), and Continuous Treatment with scheduled flush intervals. These options provide flexibility to adapt to specific operational needs.
DCBatch dynamically adjusts batch amounts in response to changes in production or process variables. Technicians can remotely update treatment setpoints through the DC3 Portal, allowing for real-time optimization without waiting for the next truck treating cycle.
Yes, DCBatch integrates seamlessly into SCADA systems and also works with pump-off controllers. This integration allows for autonomous management of batch programs and ensures real-time data and control of chemical dosing processes.
By reducing the frequency of truck trips to remote locations, DCBatch minimizes Health, Safety, and Environmental (HSE) risks, lowers environmental impact, and reduces the potential for bacterial contamination associated with truck flush water.
DCBatch is designed to be versatile and can work with any type of pump or tank. This flexibility makes it suitable for a wide range of setups, ensuring it meets the specific needs of different operations.
The DCBatch system includes a voltage compensation algorithm to maintain accurate dosing rates even when supply voltage varies. This feature requires an initial calibration at different voltage levels to determine the necessary adjustments.
Yes, DCBatch includes 24/7 tank level monitoring to provide real-time visibility into chemical levels, helping to avoid run-outs and ensuring consistent treatment.
Absolutely. DCBatch is ideal for remote locations where monitoring is essential to maintain effective treatments. The system’s automated and remote-control capabilities reduce the need for on-site adjustments and allow for proactive management.
Calibration of the DCBatch pump is conducted through a manual drawdown procedure. The system records initial and final levels as the pump operates, calculating a pump factor based on the difference. Technicians can accept or repeat the calibration as needed to ensure accurate performance.
Calculate Your ROI
Typical return on investment is seen anywhere from 3 days to 3 months